Ultrasonic inspection is one of the most widely used NDT technique for both volumetric and surface flaw detection and evaluation. It’s capable of provide dimensional measurements, material characterisation, amongst others uses. Ultrasonic testing utilises high-frequency signals ranging from 500kHz to 20MHz, high voltage pulses are converted from electrical energy into ultrasonic waves, which then propagate through the material undergoing inspection.
Inspection Technique
Ultrasonic Testing (UT)
Sonomatic is a leader in specialised ultrasonic inspection solutions offering a wide range of techniques including automated corrosion mapping and shear wave, TOFD, PAUT, LRUT, Multiskip and CHIME. Inspection applications include NII (non-intrusive inspection), thickness profiling/corrosion mapping, critical weld inspection, WRE (weld root erosion), FMD (flooded member detection), contact point corrosion/CUPS, and inspection of various damage mechanisms including fatigue cracking, HIC, SCC and carburisation to name a few.
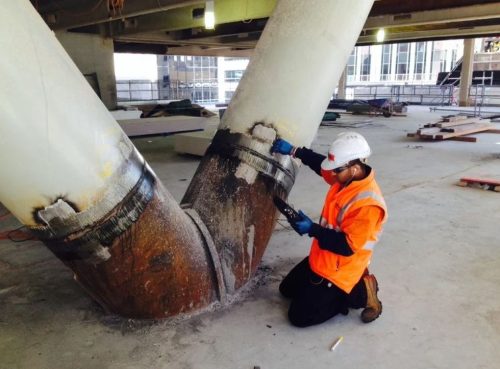
- Immediate results are achievable, enabling swift decision-making processes
- Capable of accurate defects' size, shape, orientation, and characterisation
- Provides greater accuracy in measuring the depth of internal flaws and thickness of components with parallel surfaces, compared to other NDT methods
- Only limited access required in many instances
- Non-hazardous to operators, equipment, or surrounding materials
- Capable of detecting extremely small flaws
- Highly automated and portable operations in most cases
- Inspection capable a variety of materials
Time-of-Flight Diffraction (TOFD)
Time-of-Flight Diffraction (TOFD) is a highly accurate ultrasonic inspection technique used to detect and size flaws in welds and critical structural components. It operates by capturing the diffraction of ultrasonic waves from flaw edges, offering greater precision in defect characterisation compared to conventional UT methods. TOFD delivers high probability of detection (POD) and superior sizing accuracy, making it ideal for applications where reliability is paramount.
Sonomatic is a leader in advanced ultrasonic inspection solutions, offering TOFD as part of its comprehensive service portfolio. The technique is applied in weld integrity assessments, fabrication and in-service inspections, defect monitoring, and accurate sizing of crack-like flaws. TOFD is especially effective for identifying planar defects such as lack of fusion, incomplete penetration, and fatigue cracking—common challenges in the oil and gas, power generation, and infrastructure sectors.
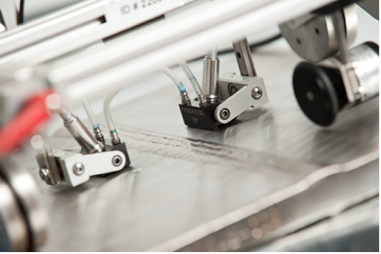
- High accuracy in defect detection and sizing, reducing reliance on radiography
- Fast and efficient scanning with real-time data acquisition
- Minimal sensitivity to probe misalignment, enhancing reliability
- Provides permanent digital records for post-analysis and repeatability
- High probability of detection (POD) for critical weld defects
- Suitable for both new construction and in-service inspections
- Reduced access requirements compared to traditional radiographic methods
- Safe and environmentally friendly with no radiation hazards
Phased Array (PA)
Phased Array is an advanced ultrasonic technique used in the industrial sector, offering enhanced information and visualisation compared to conventional non-destructive ultrasonic testing methods.
PAUT corrosion mapping increases productivity and enables the collection of high-resolution data through fully encoded C-scan imaging. This approach effectively identifies wall thickness loss due to corrosion, abrasion, erosion, and bonding issues, and supports the detection of mid-wall damage such as hydrogen-induced cracking, blistering, and manufacturing-induced laminations.
Beamforming PAUT involves manipulating the timing and amplitude of ultrasonic signals from an array of transducers to generate and control the direction, focus, and shape of the ultrasonic beam. Recent advancements, such as Full Matrix Capture (FMC), allow for the recording of every transmit-receive combination within a phased array transducer, significantly improving defect characterisation. These techniques offer exceptional flexibility and efficiency for inspecting welds and other critical components, and are well-suited to applications including complex geometry, flange face corrosion, bolt inspections, high-temperature hydrogen attack (HTHA), stress-oriented hydrogen-induced cracking (SOHIC), and stress corrosion cracking (SCC).
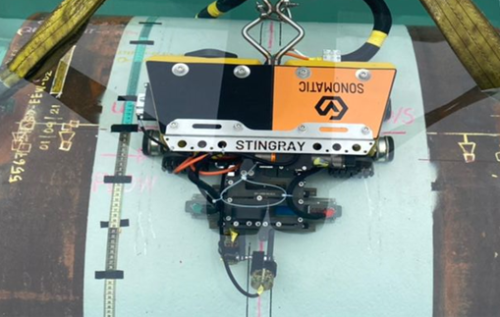
Sonomatic provide everything from ‘off the shelf’ to bespoke fully automated PAUT solutions. Key Benefits Include:
- Electronic beam manipulation allows more precise inspection of components
- Involves the physics of ultrasonic testing and utilises modern computing and electronics to produce highly complex inspection capabilities
- Reduced inspection times/improved efficiency
- Improved accuracy and sensitivity increasing the POD and sizing capabilities
- Increased reliability and repeatability
- Simplified inspection of complex components
- Improved imaging and permanent electronic record
Magnetic Eddy Current (MEC™)
The next generation MEC™ technique is a fast and reliable method for the detection of corrosion and defects in pipes, pressure vessels, and drums. Applied during the process conditions, the MEC™ technique ideally supports the Non-Intrusive Inspection (NII) strategy.
MEC™ (Magnetic Eddy Current) is the next generation and a further development of the industry proven fast corrosion screening SLOFEC™ technique.
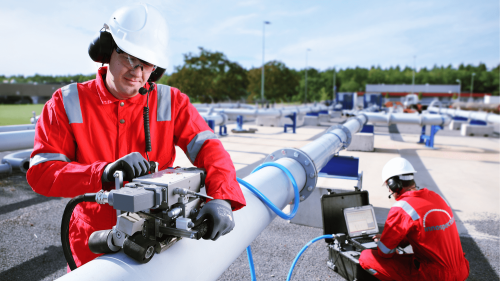
- High sensitivity and reliability in detecting topside and underside / internal and external defects including small and shallow pitting caused by bacterial corrosion (from Ø >3mm and 10% wall loss).
- Direct sizing of defects during scanning without the need for Ultrasonic verification with accuracy of +/- 10% for onsite reporting and +/- 5% for special offline analysis.
- No coating removal for a faster and more economical inspection operation.
- Ability to inspect through higher wall and coating thickness.
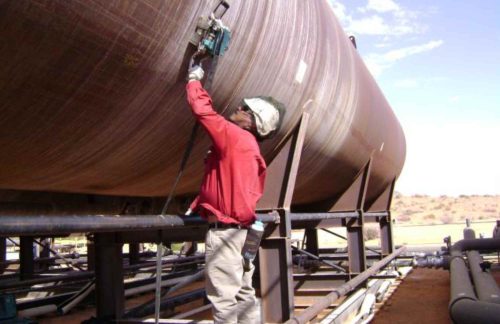
- Analysis of defect severity in terms of volume and wall loss.
- Differentiation of defects from non-defects such as inclusions and laminations.
- Enables fast and efficient scanning and C-scan mapping of large areas.
- Low cleaning requirement prior to inspection.
- Ability to inspect under various temperatures.
Dynamic Response Spectroscopy (DRS™)
Inspection of steel through coatings such as composite repairs, corrosion protection tapes and subsea insulation, is not possible with standard ultrasonic inspection methods.
In many situations, other inspection techniques such as Pulsed Eddy Current and Radiography cannot achieve the necessary sensitivity or measurement accuracy. To address this requirement, Sonomatic developed Dynamic Response Spectroscopy (DRS™); an innovative ultrasonic inspection technique for mapping corrosion through challenging coatings. Low-frequency ultrasound (<1 MHz) penetrates the coating and excites the steel, causing it to vibrate at its natural frequencies.
Using advanced signal processing algorithms, these frequencies are extracted and used to determine the steel wall thickness profile. The thickness measurement accuracy is typically ±0.5 mm.
The DRS™ technique is also used to evaluate the integrity of coatings, specifically composite repairs. Flaws such as disbondment contain small air pockets which block transmission of the ultrasound into the steel. DRS™ detects these flaws where the steel response signal is lost. Flaw acceptance criteria and QA test software have been developed by Sonomatic based on Finite Element models.
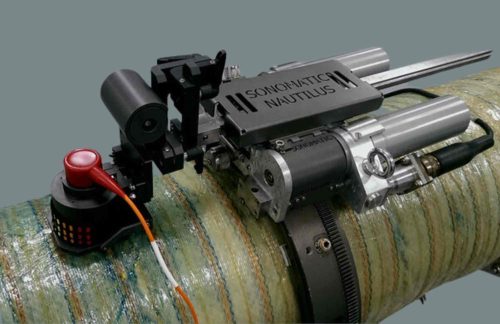
- Locating composite repair flaws such as delaminations, wrinkles, contamination.
- Input to Sonomatic QA test software to assess repair integrity.
- Confirming the absence of steel degradation.
- Estimating corrosion growth rates.
- Quantifying the extent of steel wall loss.
- Determining if corrosion growth is active.
- Input to Fitness for Service assessment, including Level 3 using Finite Element Analysis.
Pulsed Eddy Current (PEC)
Pulsed Eddy Current (PEC) is a comparative technique whereby advanced processing of the eddy current signal decay and comparison with a reference signal, allows for the determination of the average wall thickness (AWT). This fast screening method allows for the assessment of the general condition of structural steel and is best suited for general corrosion type defects in pipelines.
Sonomatic uses the Lyft Pulsed Eddy Current Array (PECA), a probe that utilises 6 units operating in tandem. Covering a 457mm wide strip, this unit greatly increases productivity and reduces set-up time.
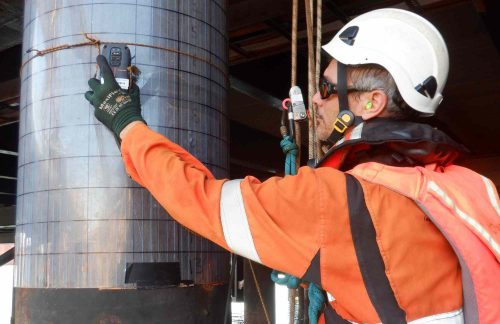
- Concrete weight coating
- Challenging Coatings
- Marine Growth
- Insulation
- Corrosion Product
- Fireproofing
High Temperature Hydrogen Attack (HTHA)
HTHA is a damage mechanism caused when steel is subjected to atomic hydrogen under elevated temperatures and pressures. Under certain conditions hydrogen atoms can dissolve into methane, forming bubbles that interconnect to generate micro-fissures along the steel grain boundaries. These micro-fissures diminish the strength of the metal, leading to the development of cracks. High-temperature hydrogen attack (HTHA) cracking has the potential to result in the complete failure of essential steel components, including welds, piping, exchangers, and other critical equipment.
With over three decades of experience in non-destructive evaluation (NDE) in the field of hot hydrogen damage, Sonomatic has amassed valuable expertise. The company has engaged in extensive technique development, validated through metallography. Sonomatic also actively participates in API working groups, contributing to the authorship of sections in API 586 Recommended Practice for the inspection of high-temperature hydrogen attack (HTHA).
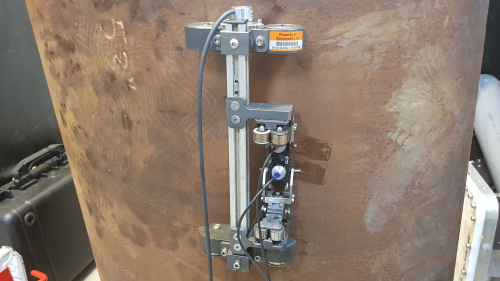
- Early detection of hot hydrogen damage
- Reduced risk to HSE and asset integrity
- Specialist ToFD frequency filtering unique to Sonomatic Microplus hardware
- Multiple PAUT and ToFD Level 2 and 3 personnel have participated in the Lavender International HTHA course, additionally technicians are trained, assessed for competency and certified internally
- Techniques have been developed for the inspection of various geometries, including flanges of various sizes, nozzles and weld-o-lets
- Multiple pressure vessel and associated pipework HTHA projects are conducted every year worldwide
Other Techniques Include:
Ultrasonic testing utilises sound waves to detect corrosion within materials. This type of NDT is utilised for long stretches of materials such as pipelines.
Multiskip is an ultrasonic rapid screening technique for corrosion and erosion detection on subsea pipelines ≥4” diameter. It uses two transducers mounted on wedges in a pitch-catch to send angled shear wave beams through the pipe wall by skipping multiple times off the ID and OD surfaces. The system is capable of high-speed, high-resolution data collection. For corrosion, loss of signal amplitude, reduction in signal arrival times, and changes to signal shape are used to provide qualitative and quantitative information.
Sonomatic has developed a technique (microwave) that can be used to inspect the outer sheath and surface or the metal armour bands of flexible pipes, plastics and composites. The technique uses low-power microwaves, which can penetrate semi-conducting materials where other NDT inspections i.e. Ultrasonic or Eddy Current inspections, are ineffective.
Sonomatic have developed an electromagnetic acoustic transducer (EMAT) system that uses horizontally polarised shear (SH) waves to inspect thinner-walled pipes. This applies to inspection at pipe supports and also for rapid screening of piping for detection of corrosion. The system is compact, battery-powered and does not require couplant, making it extremely portable.
CHIME is an advanced ultrasonic screening technique designed for rapid, large-area corrosion detection. It enables efficient, single-pass inspections without requiring costly shutdowns or dismantling, making it ideal for production vessels, pipelines, and inaccessible areas such as under pipe supports. Developed within the HOIS joint industry project, CHIME provides percentage wall loss values to identify corrosion-prone areas and has been validated through blind trials, achieving a probability of detection of 1 with zero false calls. This technique is a valuable complement to other ultrasonic methods like Multiskip and SH-EMAT, offering high detection reliability for defects with over 10% wall loss.