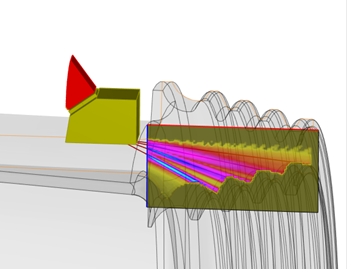
Ultrasonic inspection is widely used in the oil and gas, nuclear and energy sectors to determine the condition of equipment.
In general, the objective is to identify and, if possible, quantify any degradation or defects that have the potential to threaten the integrity of any equipment.
There is also an increasing emphasis on determining the performance of an inspection campaign.