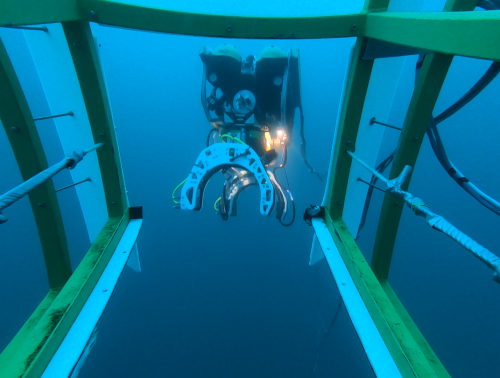
Sonomatic has a long history of providing specialist inspections that deliver quality data on pipeline conditions. Our approach is to provide data and analysis that maximises the value of the inspection to the client. We can deliver our pipeline inspection services both topside and subsea.
Pipelines are key assets for operator companies and continued pipeline integrity underlies successful business performance. They are essential to oil and gas production and failures or unplanned downtime can have a major impact on company revenues. Failures can also have severe pipeline safety and/or environmental damage consequences.