A client has a jacket structure that when manufactured, had access window cut into the jacket to allow internal backfill welding to be conducted. These Access windows are of differing geometries so no two welds are the same, but as part of the structural integrity plan, they require regular inspection for the identifying of cracks emanating from the apex region of each weld.
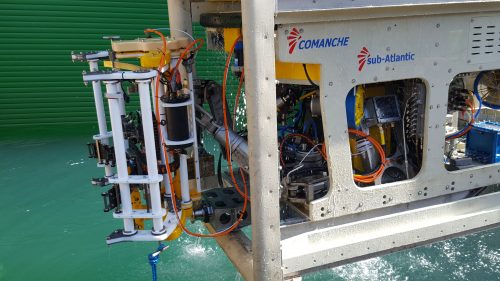
Access Window Weld Inspection Case Study
Challenges
The Access windows are all of slightly differing, geometries so no two are the same. They are not all at easily accessible locations on the jacket, so deployment to the inspection region is challenging. Placement of the tool requires a good deal of accuracy. The client required the inspection to be conducted via the platform from a small work class type ROV such as a Sub Atlantic Comanche class eliminating the need for divers, or a vessel.
Outcome
Sonomatic designed and develped a bespoke 4 axis Window Access Scanner that is ROV deployable from the platform from a Comanche ROV. The tool utilised some very bespoke designs, and software to inspect the apex of each window weld with TOFD and AUT Shear wave for 250mm either side of this region.