An inspection was required on a production separator to give confidence that no flaws were present within a nozzle weld following a dynamic loading event. Due to the position of the nozzle on the domed end, the profile of the weld varies around the circumference of the nozzle. Sonomatic were approached to validate the capability of the inspection approach.
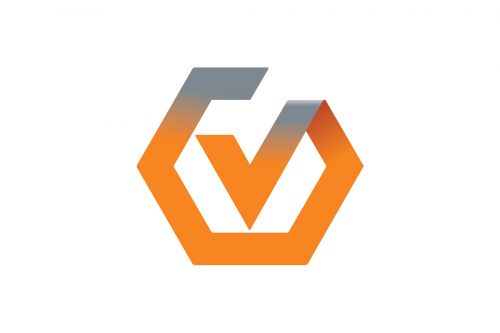
Civa Modelling of the Inspection of a Nozzle to Domed End Weld on a Production Separator Case Study
Process
To validate the inspection that was completed on the nozzle, cross sections based on the geometry of the nozzle (Figure 1) were created in the Civa modelling software (an example is shown in Figure 2).
Flaws were placed at several locations within the nozzle weld and results were simulated using a selection of shear wave angled probes (Figure 3 shows the results from a single scan).
The results were used to determine an inspection strategy that would provide the greatest probability of detection for the flaws under consideration.
Outcome
Analysis of the results determined the likelihood of detection for each of the flaws within the weld and was used to validate the inspection techniques applied to the nozzle. The use of modelling allowed the techniques to be developed rapidly with confidence in capability provided before deployment offshore.
This allowed a rapid deployment of the inspection with confidence in capability.
Downtime before the separator was returned to service was thereby significantly reduced and the operator benefited through minimisation of associated lost production. The Civa modelling, along with the inspection results obtained, formed a key element of the operator’s case for continued operation.