A client required an ROV deployed high resolution corrosion mapping inspection for 360° circumferentially, and along the full length, of 8”, 10.75” and 12” Duplex steel Gooseneck bends and elbows at water depths of up to 1400m. This was an urgent request with only a 6-week window to develop a complete solution.
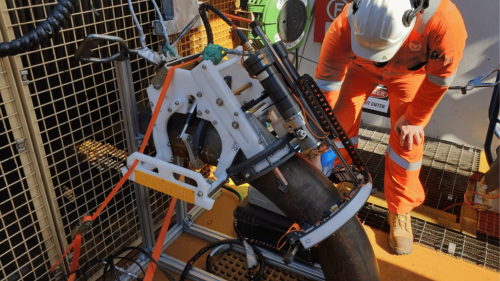
Gooseneck Bend Inspection
Process
The timescales to deliver a field practical solution were limited. Due to the various diameters and geometries that were to be inspected, any tooling would have to be readily adaptable to accommodate. The solution was to be ROV deployable, robust, provide accurate positional feedback and ultrasonic thickness measurements.
Outcome
To expedite the development, the solution was to design and fabricate a bespoke variable diameter scanning frame to deploy a Sonomatic Nautilus dual axis scanning system with hydraulic clamps and dual inspection heads such, that full 360° coverage could be achieved. The data presentation software was enhanced to correct the data for any curvature effects.
The solution provided accurate circumferential and axial encoded feedback to provide detailed corrosion maps of the full-lengths for each bend.