A client operated a number of subsea pipelines in dry gas service. These lines were not designed for in-line inspection but had been in service for some time and a validation of their condition was necessary. The inspection to validate condition was, therefore, to be performed using externally applied tools.
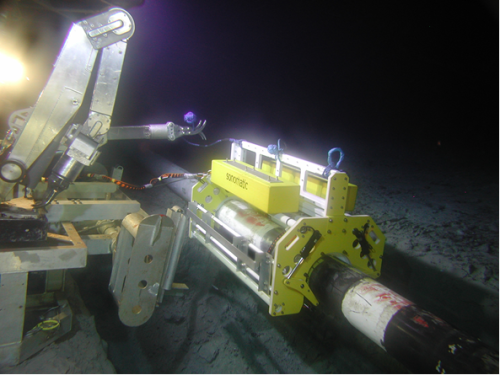
INSPECTION AND INTEGRITY ASSESSMENT ON UNPIGGABLE DRY GAS PIPELINE SUBSEA
PROCESS
The operating conditions and material for the lines was such that internal corrosion was not expected. The aim was therefore to validate absence of corrosion and to demonstrate a very low probability of degradation with the potential to threaten integrity. A sampling inspection approach was adopted, with the sample regions
being selected on the basis of highest susceptibility to degradation based on detailed corrosion studies carried out by the client. Inspection performance requirements, with respect to accuracy and probability of detection (POD) were defined so as to ensure the low coverage inspection would provide a sufficient basis for statistical validation.
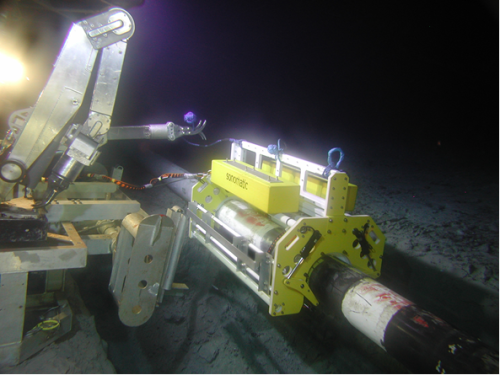
The subsea inspection was carried using Sonomatic’s accurate 0 degree corrosion mapping technique delivered by its ROV-iT ROV deployed scanner. This inspection provided accurate wall thickness measurements with a high probability of detection (POD) for low level degradation.
Detailed analysis was performed on the inspection data to validate that the performance achieved met the requirements and that there was no evidence of any in-service degradation in the regions scanned.
The inspection parameters and results were then used in a Bayesian statistical analysis to make estimates for the probabilities related to minimum thickness for the lines as a whole. The analysis indicated probabilities less than the limiting values, thereby providing assurance of the integrity of the lines.
OUTCOME
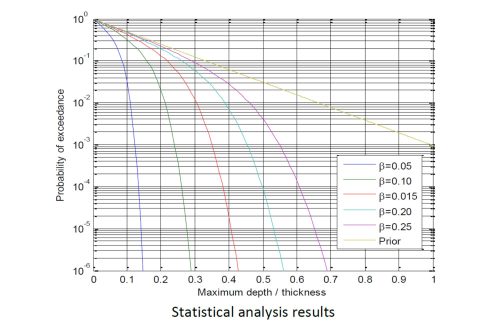
The inspection and analysis performed by Sonomatic provided validation of the condition of the lines without the need for expensive modifications to facilitate in-line inspection. The inspection performance (accuracy and POD) delivered were critical in allowing validation based on a low coverage inspection. This, together with the use of ROV rather than diver deployed inspection, reduced the time and cost of the validation exercise.