Sonomatic was requested by its client to provide an inspection solution to enable the inspection of the underside of a square tank, using corrosion mapping. The tank configuration included cross members on the underside which required negotiating remotely, making this inspection more challenging. Sonomatic’s Equipment development team, in conjunction with the Technical Support Group, used current Sonomatic in-house inspection technology and software to provide a solution to this inspection challenge.
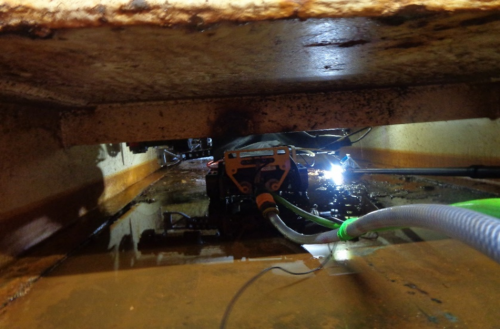
Under Tank Corrosion Mapping Scanner Success Story
Process
Existing inspection methods employed by the assets incumbent inspection company were limited to simply reaching in and obtaining random thickness measurements at arm’s length, this approach fell short of achieving the required coverage, quantity, and quality of data required in order to make integrity assessments and decision on.
The Sonomatic Equipment Engineering department, utilised our Automated Fast Scanning Raptor scanner as the base for the under tank scanner. Engineering and software development were required in order to allow the scanning to be conducted upwards rather than downwards, in addition to this the requirement, being able to negotiate the underside stiffeners was built into the hardware and software design, allowing the scanning arm to raise and lower itself remotely while negotiating these stiffeners and achieve suitable scanning coverage.
Outcome
As in all Sonomatic Non-Intrusive Inspection projects, inspection data is captured live and transposed in real-time, directly onto the 3D generated component model using Sonomatic’s SIMS program. This dramatically reduces the data management and reporting time associated with these inspection campaigns.
SIMS integrates directly with Sonomatics advanced inspection systems and scanners, allowing live build up of composites as the data is collected. This allows advanced waveform and data analysis capabilities and population of the composite directly onto live 2D & 3D models.