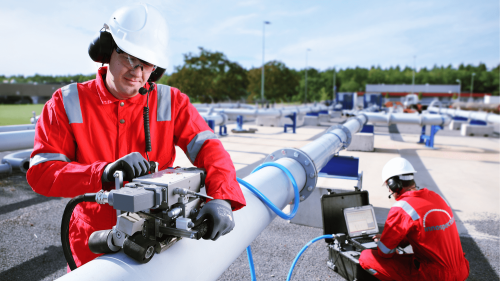
Inspection of the steel under a composite repair allows an estimation of the corrosion growth rate. Understanding the condition of the composite repairs and underlying steel means that the risk of ongoing operation is effectively managed, the cost of replacement can be deferred or avoided and production is maintained – a shutdown is not needed.