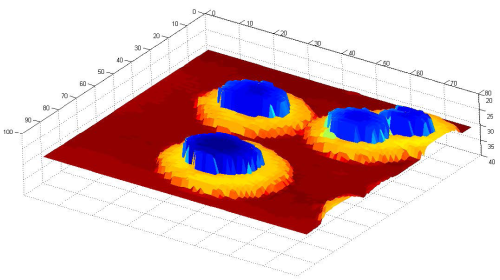
Sonomatic’s Integrity Services department provides clients with a fully integrated service from detailed inspection planning, through to the evaluation of the results and the creation of an ongoing integrity management plan. The aim is to bridge the gap between integrity and inspection activities to ensure that the client’s integrity needs are effectively met through a sufficient understanding of the real condition of equipment in service.