An Atmospheric Storage Tank (AST) had been regularly standing in water for several years. This had led to visible external corrosion. Random internal corrosion pitting had also been noted during previous internal inspections. Concerns had been raised over the possibility of coincident internal and external corrosion causing the corrosion allowance to have been exceeded. The incumbent inspection contractor had arranged to remove all corrosion product from the external surface but could only take thickness readings at isolated locations due to the irregular surface giving contact problems.
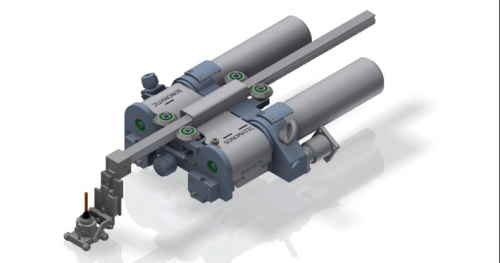
Corrosion Mapping of Externally Corroded AST Walls
Solution
Sonomatic is experienced with the evaluation of coincident internal and external corrosion through ILI verification activity of pipelines, both subsea and terrestrial. The technique involves careful selection of probe characteristics to ensure the tightest beam possible and performing automated measurements, form a stable platform using the immersion technique. In this manner, both the external and internal wall profiles can be accurately mapped.
A flexible carbon fibre composite track was attached to the tank wall with magnetic feet. The track ensured conformity in the circumferential direction whilst providing a rigid platform in the vertical plane. The ultrasonic probe was mounted a fixed distance from the external surface and coupling to the surface was achieved using a water column (bubbler). A band of measurements was collected 150 mm above the wall to annular plate attachment weld at locations where corrosion could be seen visually to be most severe.
Conclusion
In this example, the internal random pitting was shown not to be coincident with external corrosion. The minimum wall thickness was, therefore, greater than would be the case for overlapping corrosion. The high-quality data was used in a statistical analysis to estimate on a probabilistic basis, the worst-case condition. The findings of the inspection and analysis supported a case for the continued operation of the tank with no need to remove it from service for repair or replacement. This resulted in substantial business benefits to the client.
The data obtained also forms a reliable baseline for accurately monitoring future corrosion growth, thereby efficient through-life management of the tank. The data can also be exported directly into a finite element model for fitness-for-service assessment.