A pinhole leak was seen in a flange weld on a 12” Water Injection Flowline at 500m water depth. The pipe and flange were carbon steel API 5L X60 with internal CRA (Inconel 625 Corrosion Resistant Alloy) cladding and the butt weld was also CRA (Inconel) welded. The requirement was to develop pipeline inspection techniques to examine similar (10” and 12”) CRA welds/HAZ and the parent material either side for possible corrosion.
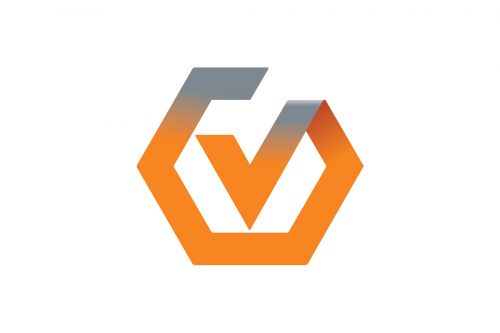
Targeted Inspection of CRA Welds on Water Injection Flanged Flowlines
Process
The inspection methodology was to apply multiple angle shear wave inspections from both sides of the weld in one deployment with full coverage (360°) of the weld and TOFD for defect confirmation and sizing when required.
The full system was validated on mockup samples prior to mobilisation to demostrate the POD and accuracies of the system.
Outcome
Without this novel inspection technology being utilised, these welds were un-inspectable, and could have caused significant unscheduled shutdowns and lost productivity. The inspection performance (accuracy & POD) delivered was critical in allowing the client to continue safe operation of the pipelines. This together with ROV deployment, reduced the time, and costs to complete the inspections.