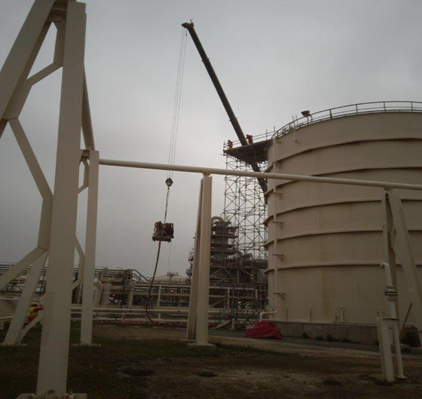
For decades, Sonomatic has been the vanguard of designing and delivering state-of-the-art inspection tools, marked by our exceptional ability to create solutions from the ground up and tailor them precisely to meet the distinct requirements of our clients. We take pride in our unwavering commitment to precision and excellence, and Sonomatic has emerged as the trusted partner in the realm of robotic inspection.
Our adaptability and versatility have become the cornerstones of our success, for we firmly believe that a one-size-fits-all approach simply does not suffice. With years of expertise under our belts, we bring to the table a wealth of experience that enables us to take projects from conception to realisation, providing unparalleled on-site proficiency every step of the way.